A sorozat előző része ott ért véget, hogy a servo tápegységének hibáját sikerült megtalálni. A servo dobozt visszavitem a megrendelőhöz és beépítettem.
A bekapcsolás előtt ellenőriztem amit kell, majd bekapcsoltam a gépet.
Bekövetkezett, amitől tartottam: a servo egység fő tápfeszültség bekapcsolása pillanatában ismét belső hibát érzékelt és letiltott.
Most viszont már – mivel az analóg rendszer tápfeszültség ellátása már rendben volt, a hibára utaló jelzés is látható volt.
Sajnos az „X” tengely hajtása a működtető feszültség rákapcsolásakor hibát jelzett.
Az „X” tengely analóg szabályozott hajtását még a gyárban szétszereltem, és egy kísérletet végeztem vele:
A hajtás alapvetően két részre tagolható: egy analóg elektronikát tartalmazó szabályozó áramkörre és egy nagy teljesítményű kimenő fokozatra.
Mielőtt hazavittem a hajtást, úgy gondoltam egy kísérlettel szűkíteni lehetne a hibakeresést: Azonos elektronikát használó másik tengely szabályozó paneljét cserélve a vizsgált készülék azonos paneljével szűkíthető a hiba. A panelt átcserélve a hiba nem ugrott át a másik tengelyre, tehát a helyben maradt teljesítmény fokozatban kellett keresni a hibát.
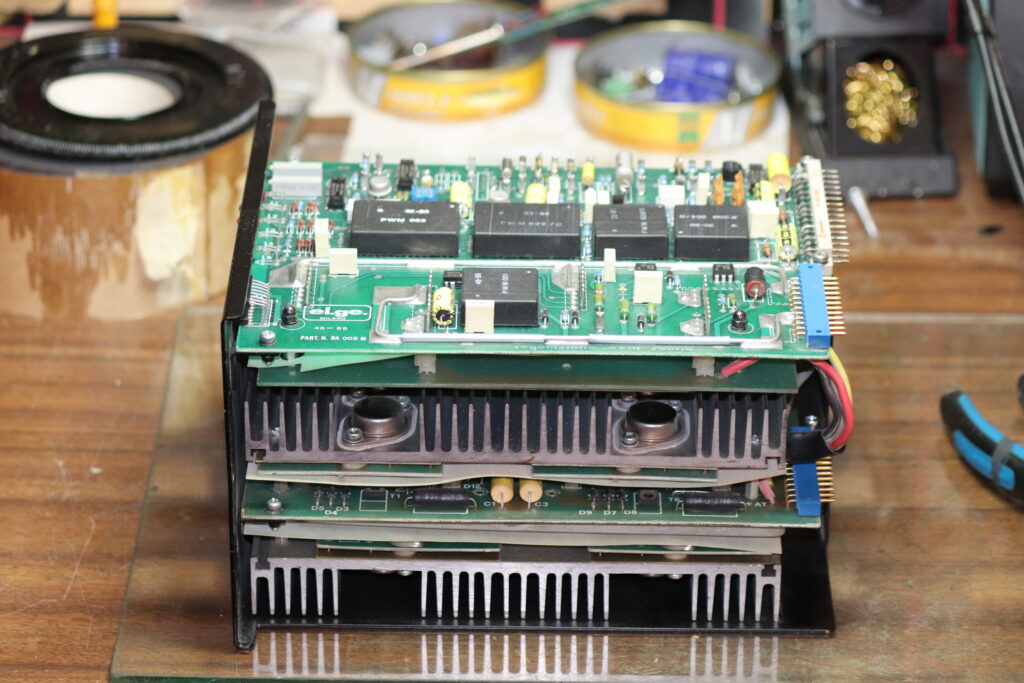
A hajtást összeraktam majd a műhelyembe szállítottam.
Felső részen a hibrid áramköröket is tartalmazó szabályozó elektronikát, alatta a hűtőbordák közt a teljesítmény fokozat meghajtását, a hűtőbordákon pedig a teljesítmény fokozatot láthatja az érdeklődő.
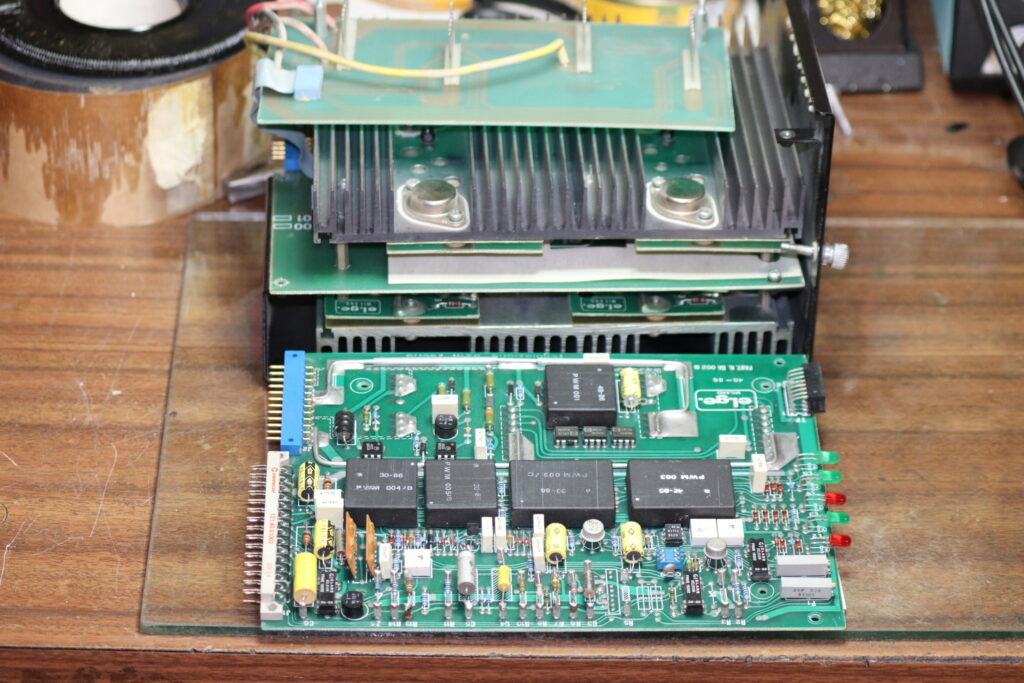
Tovább folytatva a szétszerelést bontottam a csatlakozást a teljesítmény fokozat és a szabályozó áramkör közt.
A teljesítmény fokozat meghajtását kiszereltem, és az alkatrészeket műszerrel ellenőriztem. Az ellenőrzés során hibás alkatrészt nem találtam, ezért tovább folytattam a boncolást.
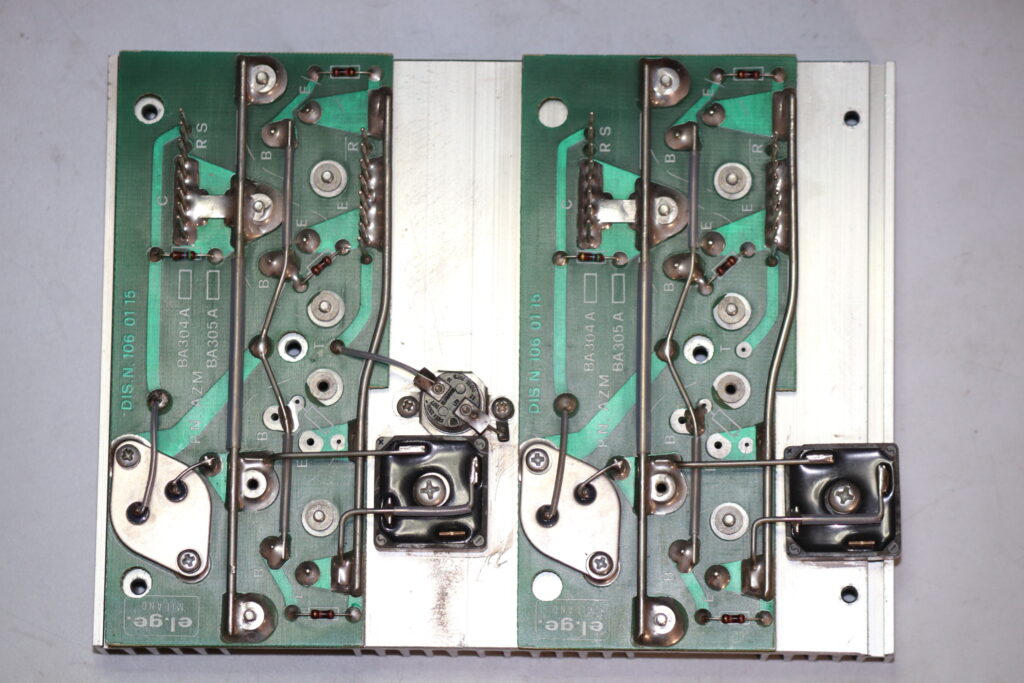
A teljesítmény fokozatok műszeres ellenőrzése következett. Először összehasonlító méréseket végeztem bontott csatlakozások mellett. (a panelt lehúztam a meghajtó panelről) Ellenőriztem a hőérzékelőket, mivel párhuzamosan voltak kapcsolva, ezért NO (normaly open) működésűként ellenőriztem. Felemelve pákával melegítés közben mértem, jól hallhatóan kattant és működött.
Ezután a kimenő tranzisztorok emitter – kollektor nyitását mértem. három áramkör esetében 0,34 voltot jelzett a műszer, egy áramkörnél viszont 0V értéket jelzett. Megvagy! gondoltam.
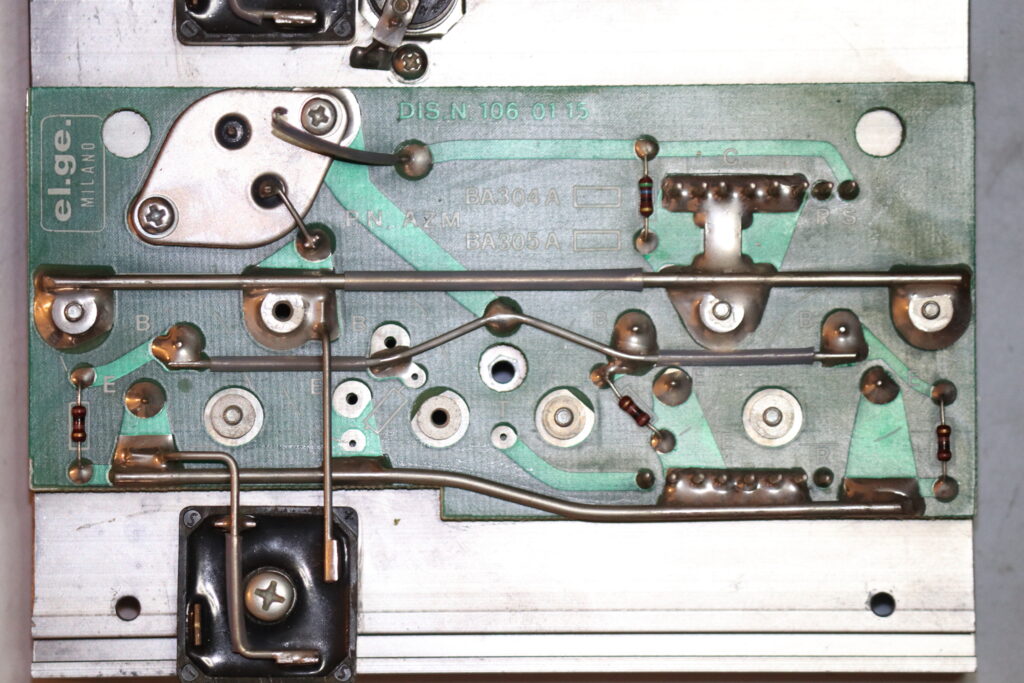
Az illető panelt gondosabb vizsgálathoz készítettem elő. Leforrasztottam a meghajtó tranzisztor emitterére menő huzalt, majd összehasonlító mérést végeztem a már jónak mért panelon szerelt alkatrésszel.
A meghajtó tranzisztor (BUW 32A) jónak bizonyult, így nem volt más hátra a zárlatos eszközt a három párhuzamosan kapcsolt tranzisztor közt kell keressem.
Ahhoz, hogy a vizsgálatot el tudjam végezni, felrajzoltam a kapcsolási rajzát egy panelnak.
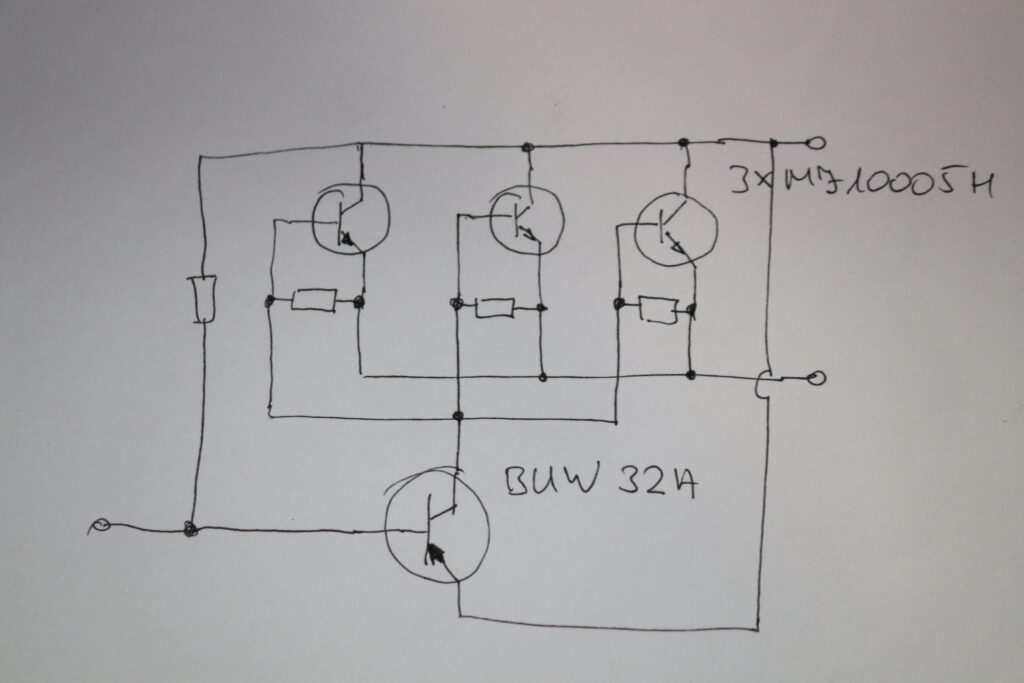
Nosza, őket is előkészítettem, szerencsére a panel egy oldalon fóliázott volt, furatfém nélkül, ezért csak a forraszanyagot kellett eltávolítani.
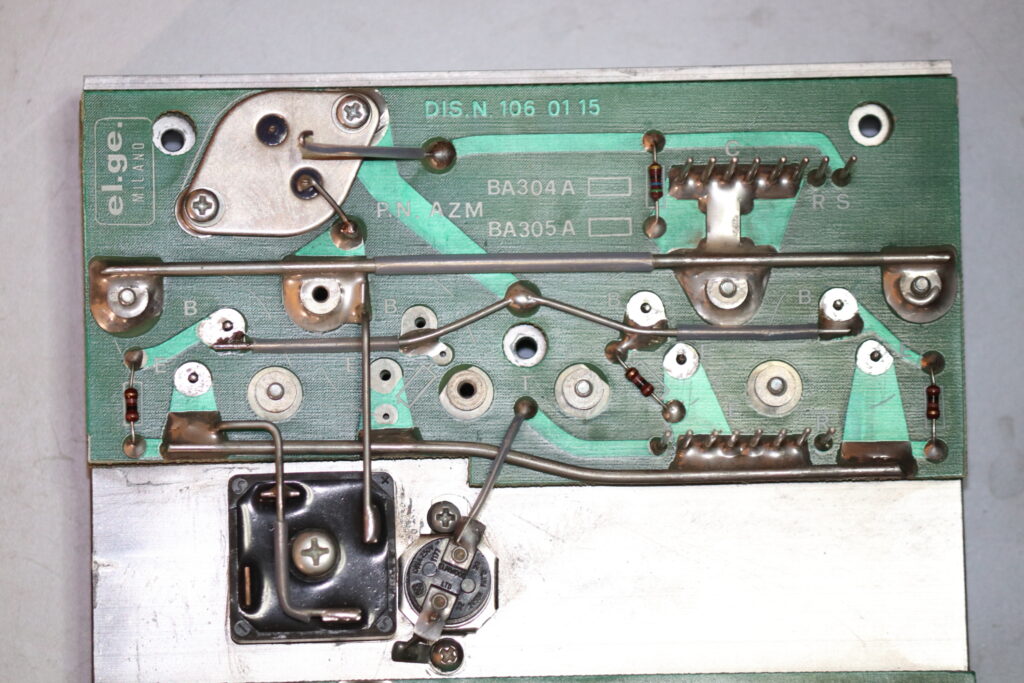
Az alkatrészek lábát furatközépre állítva el tudtam végezni a mérést. Hamar meg is lett a zárlatos példány.
Ahhoz, hogy az áramkör megfelelően működjön, szerencsés ha a párhuzamosan kapcsolt tranzisztorok válogatott példányok, és ezért mind a három tranzisztor cseréje mellett döntöttem, bár csak egy volt hibás. Amíg az alkatrész megérkezett, az analóg szabályozási rész egyes alkatrészeit vizsgálgattam.

A tápfeszültség zaj és zavar mentesítését végző 220uF kapacitású elektrolit kondenzátorait vettem górcső alá. Ahhoz hogy a kondenzátorok hatékonyságáról meg tudjak győződni kapacitás mérést végeztem. A mért értékek kismértékben a névleges érték alatt voltak.
Ezután a kondenzátorok ESR értékeit mértem meg, ami 2.1 – 2.4 ohm között voltak. Ezek bizony már fáradtak, gondoltam, mivel egy új jó minőségű, azonos kapacitású elektrolit kondenzátor ESR értékét 0,07 ohm közelében mértem átlagosan.
Az alkatrészek megérkezése után nekiláttam a kiszerelésnek, és az új példányok beépítésének. A hővezető pasztát eltávolítottam a hűtőfelületről és a csillámlemezről is.
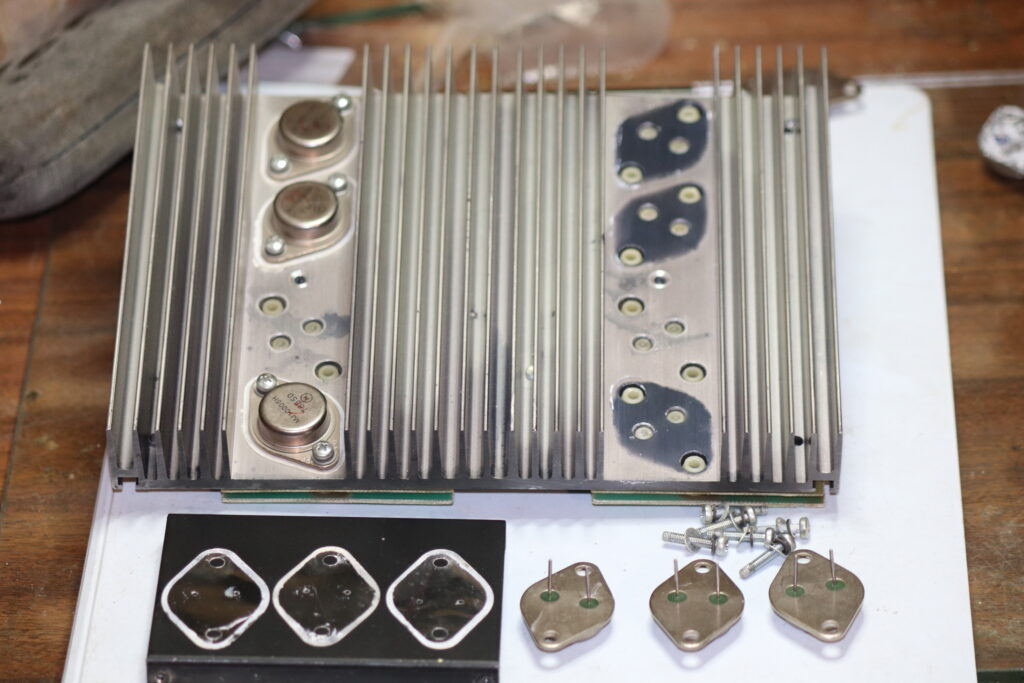
Az előkészített alkatrészeket bepasztáztam, majd felszereltem a hűtőbordára. A csavarkötést többször utánahúztam óvatosan, hogy a pasztának legyen ideje kijönni, majd beforrasztottam az alkatrész lábait.
A beforrasztás után már alig bírtam a bőrömbe férni: szabadságot kértem a munkahelyemen és inaltam másnap beszerelni.
Az eredményben nem csalatkoztam: a gép pöccre röffent! Beindult – és ennek nagyon örültem.
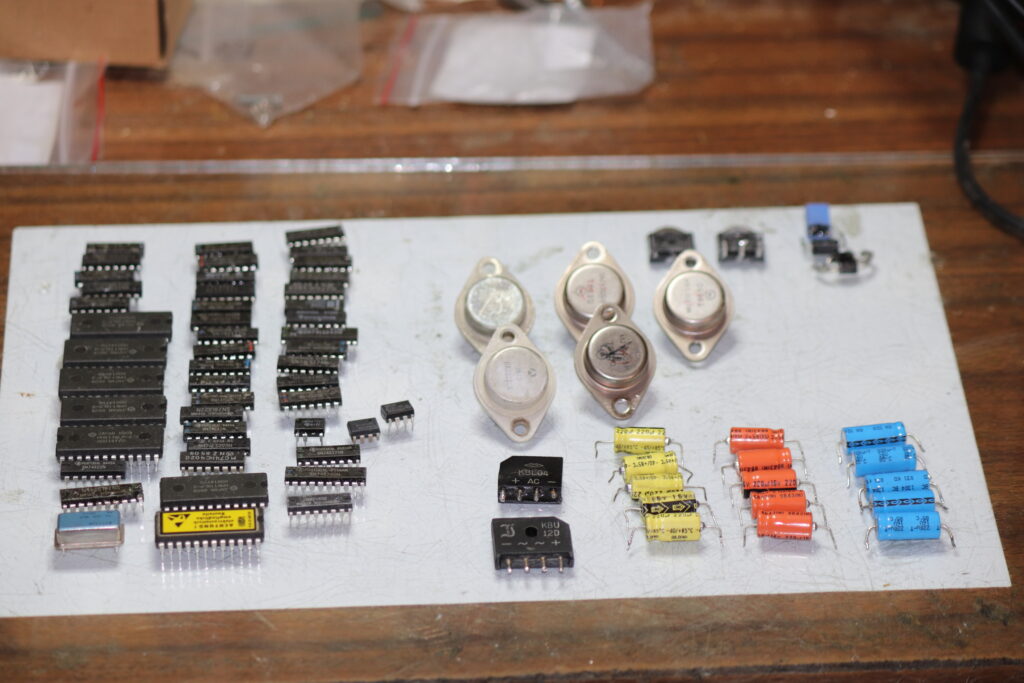
A javítás során kitermelt hibás alkatrészek – amik megmaradtak láthatóak. Volt idő amikor már majdnem feladtam ezt a projektet, és kidobtam néhány IC-t, és egy elromlott ventilátort, így a teríték nem teljes.
Számlát írok, és csak remélem legközelebb könnyebb dolgom lesz.